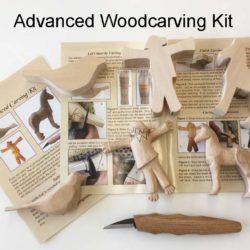
Many artists are starting to explore the art of wood carving with a chainsaw. The art is a natural extension and extension of their skill sets. It often involves a combination or modern and traditional carving techniques. Crager and Tracie, his wife have been carving wood masterpieces since the 1960s. In between shows, they try to get home as much as possible to help out with painting and staining. His daughters are now involved in his work as well, helping out on occasion with painting or staining. They prefer white pine because it is lighter than other types of pine and is less likely to crack.
Rich Anderson
Rich Anderson is a chainsaw wood carving artist from Reedsport. Anderson, a Poughkeepsie-native, lives with his family. Anderson has several degrees from the Fine Arts Department and teaches art to children from Pre-K through Fifth Grade. He has carved many sculptures around Long Island and has even created sculptures in Colorado. His works include sculptures made from corn ear and standing trees. He is currently working with Youngs Farm sign in Riverhead.
He is able to create exquisite sculptures using a $400 chainsaw, which would normally take several days to chisel a tree. Chainsaw wood carving is also a greener choice than chisels and hammers because they are recyclable. Anderson advertises his business through word of mouth and has carved a giant cobra and a great blue heron for a mechanic in Wading River.
Tracie Dugas
Tracie Dugas's impressive work as a chainsaw woodcarver is evident in the life-size wizard she carved out of wood. The young woman, 49, lives in Clare, Nova Scotia, between Digby and Yarmouth. The chainsaw woodcarver was one of many artists who presented their work during Canada Day Weekend in Sydney, Nova Scotia. While Sydney's waterfront was full of tourists, the brief dry spell gave locals the perfect opportunity to enjoy the waterfront and get a glimpse from the chainsaw wood carver.
Tim Crager
While Tim Crager didn't consider himself an artist and was only moderately talented with a chainsaw, his passion for carving turned into a full-time career six years ago. Since then, Crager has traveled the Eastern U.S., selling more than $1 million worth of carvings. Crager was born in Garrett, Eastern Kentucky. He grew up watching the chainsaw wood carver at his work. Crager was attracted to the art's unique style and he gave his boss his two-week notice.

Crager prefers white pine when it comes to wood choice. It's readily available from tree trimming businesses. But, there are many wood types that people prefer. Crager will follow the grain of the wood to create his pieces. While Crager usually knows exactly what he's going to make before he begins a project, he will often change his mind mid-project. A small project can be done in an hour, while a large one may take 33 to 35 hours.
Don Scoggins
Don Scoggins works as a chainsaw-woodcarver. His wood carvings include detailed animals and often include multiple animals. His creations have attracted attention from tourists and neighbors alike. The chainsaw sculptures are so large and detailed that they adorn the entrance and coffee shop at Blue Arrow Farm. Blue Arrow Farm's owner is Don Oriolo. He also manages Felix the Cat. Don Oriolo and his wife, Kacie, met while competing in a chainsaw competition at the New Jersey State Fair.
The 15-year-old wood carver and winner of the award was inspired to start carving at a Reedsport competition. He was already skilled at carving by hand, but had never used a saw before. His latest carvings feature an otter with a mother beaver and a squirrel peering out of the tree. And now, he's ready to compete at the National Chainsaw Carving Competition.
Dan Porter
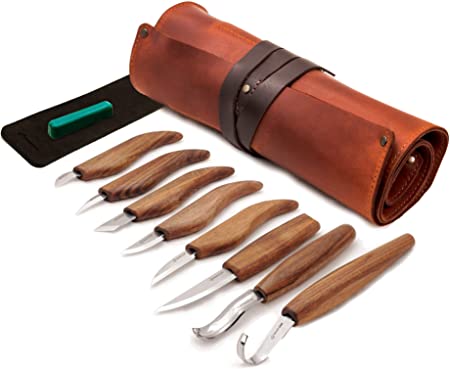
For many years, Dan Porter, a chainsaw wood carver from Oregon, has been a sought-after local talent. His intricate, detailed carvings have been admired all over the world. But before he became famous, he spent years carving for the timber industry and met other like-minded people. Here are some of the qualities that made him a world-class Wood Carver:
FAQ
Where do I get my woodworking supplies?
There are many places you can get everything you need, and you don't have to go far. You could shop at your local hardware store or go online to Amazon.com.
You might also consider flea markets and garage sale for any old furniture or other materials you could reuse.
You can learn how to woodwork.
It is best to do it yourself. Woodworking is an intricate art form that requires practice, skill, patience, and experience. To master any craft, it takes time.
It is the best way to learn to do something is to actually do it. Start small and learn from your mistakes.
Are there any other things I should know regarding woodworking?
Furniture making is a laborious task. It's easy not to appreciate how hard it is. The hardest part of the process is actually finding the right wood. It can be hard to choose from the many types of wood that are available.
A problem is that wood doesn't have the same properties. Some woods will crack or warp with time. Others will split or crack. These are important considerations to make before you purchase wood.
Is it possible to refinish your own furniture?
Yes! You don't have to hire a professional to refinish furniture. There are many ways you can do it yourself. Here are some suggestions:
Use sandpaper to remove scratches and stains. Use a clean cloth to wipe the surface.
Apply clear polyurethane paint. Allow to dry thoroughly before moving furniture.
Use acrylic paint to paint furniture.
You can stain the furniture instead of using paint. The stain will give the furniture a rich look.
Use shellac wax. Applying wax will give the wood shine and protection.
What is the difference between a hobbyist or a professional woodworker, and how can you tell?
Hobbyists are passionate about making things from wood, while professionals tend to be more focused on the quality and craftsmanship of their work. Hobbyists often take pride in the creations they make and often share them to family and friends. Professionals will spend hours researching designs before they begin working on a project. They'll pay great attention to details, from choosing the most suitable materials to finishing the work perfectly.
How often should new supplies be purchased?
You'll probably have to replace some of your tools over time. Sharpening hand tools is a must. Power tools will require replacement parts every so often. To avoid buying too much at once, try to spread your purchases out over a few months.
Which wooden items are very popular?
Wood that has been harvested sustainably is the best-selling type of wood.
Most furniture is made from oak, maple, mahogany or walnut.
These woods are extremely strong but also have beautiful colors and grain patterns. They are also very durable if properly maintained.
Wooden furniture should always be painted first to protect against moisture damage. This includes all surfaces, including drawers, doors, and handles.
Paint that is water-resistant will ensure furniture lasts for a long time.
Followed by two coats, you should apply a quality oil-based primer. It is possible to apply multiple coats depending on how heavy the wear.
Avoid spray cans or aerosol colors. These products are contaminated with solvents, which evaporate rapidly and can leave behind toxic fumes.
Statistics
- Overall employment of woodworkers is projected to grow 8 percent from 2020 to 2030, about as fast as the average for all occupations. (bls.gov)
- If your lumber isn't as dry as you would like when you purchase it (over 22% in Glen Huey's opinion…probably over 10-15% in my opinion), then it's a good idea to let it acclimate to your workshop for a couple of weeks. (woodandshop.com)
- Average lumber prices rose about 600 percent between April 2020 and May 2021. (familyhandyman.com)
- In 2014, there were just over 237,000 jobs for all woodworkers, with other wood product manufacturing employing 23 percent; wood kitchen cabinets and countertop manufacturing employing 21 percent. (theartcareerproject.com)
External Links
How To
How to make wood joints
This tutorial will show how to join 2 pieces of wood together. We'll use the "pocket hole joint," which means we drill holes in the wood and then glue them together. If your wood has a straight grain, smooth surface, you can use this method. Dowel joinery might be a better option if your wood is not straight or flat. These are the steps
-
Drill Pocket Hole Joints. Measure and mark the location where you would like to place the pocket hole joint. You will then drill 3/4" deep holes through each piece of wood with a jigsaw, handheld drilling machine, or hand-held drill.
-
Sand Smooth. The wood's edges can be sanded to prevent splitting.
-
Glue Together Apply glue to both the ends of the wood. Let the wood sit for 5 minutes, then clamp it together.
-
Connect the pieces. After the glue has dried properly, clamp the pieces together to make sure they are flush.
-
Trim Joinery. Trim any excess wood surrounding the joint once the glue has dried completely.
Make sure to leave enough room between the pieces so that you can turn them inside and out.