
Whittled wood can also be used in many other ways. This article focuses on carving with whittled, but it also covers the best techniques for making flowers and utensils. Here are some suggestions to get you started. Although softwoods are easiest to whittle you can progress to harder woods when you're more skilled. Wood with straight grain is easier to whittle.
Carving whittled hardwood
Whittling is among the many ways to woodcarve. It's also one of the easiest and most accessible. In fact, most people have all the necessary tools to get started. If you want to learn how to carve wood, here are a few tips to keep in mind:
Whittling refers to a technique that creates beautiful shapes and cuts in wood. This involves removing small pieces of material from larger pieces and leaving the surface textured. Some projects are smoothed completely, while others are sanded and/or scraped. In either case, the process is done by removing material from the original piece of wood, and does not involve any clamping, gluing, or joinery.
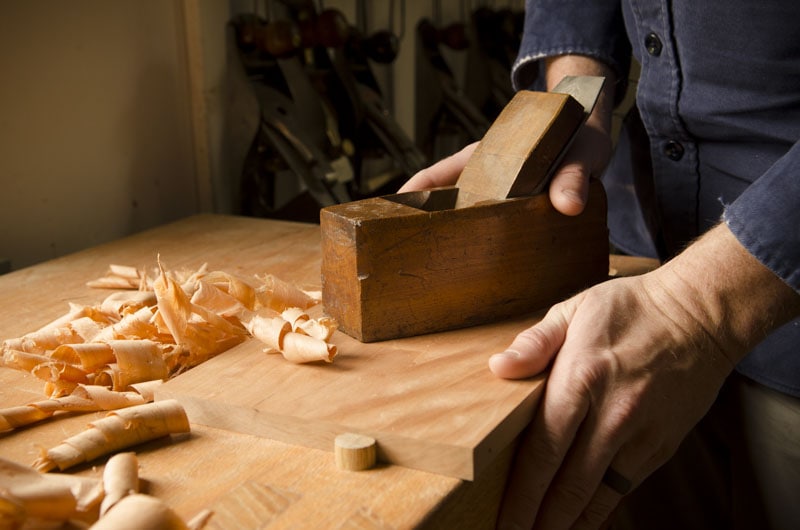
Making whittled wood utensils
Whittled wood utensils are an interesting way to use leftover pine that would otherwise go to waste. Tom used leftover southern white pine from a wine rack build to make a spoon, fork, and Japanese pull saw. He used a gouge to carve the spoon and fork shapes. Other tools included a Japanese pullsaw and a Japanese coping saw. To finish, he used some sandpaper as well as a tack cloth.
A pocketknife for whittling is an essential tool. Another essential tool is a crook and spoon knife. A folding saw, as well as a carving tool, are useful tools to remove large chunks of or small pieces of wood. Food-grade oil is also needed for finishing. Make sure to have plenty of this on hand, as the process can take an hour or two.
Whittled wood flowers
A sharp whittling blade is a good tool to use when carving a wood flower. You should always carve a flower with an angle of about 85 degrees. Your final cut should be at around 90 degrees. For more intricate flowers, you can repeat this step several times. Finally, you can display your finished flowers on a stick. You can always try another version if your first flower is not perfect.
Use boiled beeswax to give your flowers a final touch. You can also use your gouge to achieve a better finish. You should take care not to damage the wood using any of these tools. Safety always comes first. You can use different colors of petals to make the flowers. Then glue a flower pin on the back. You're almost done!
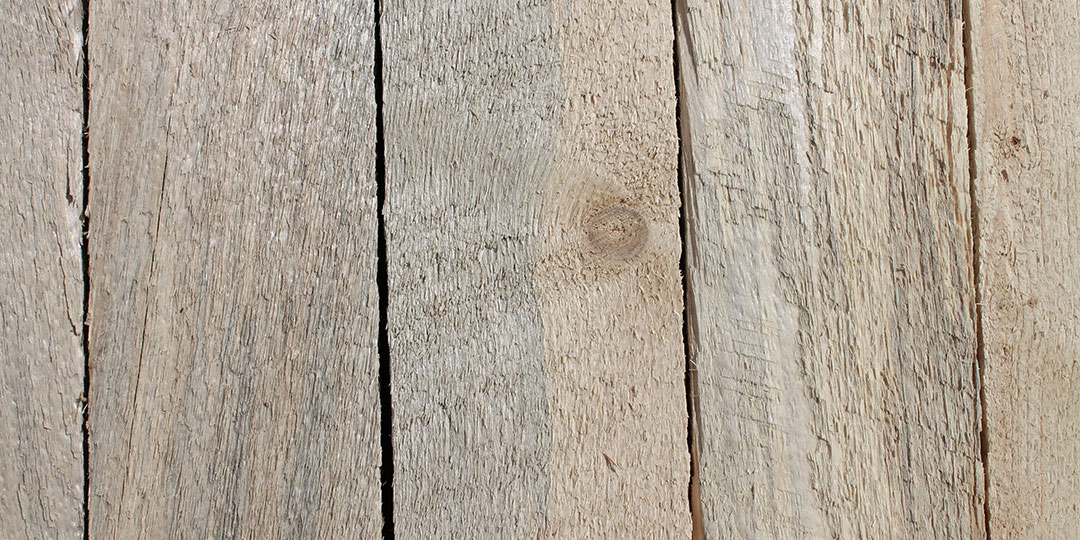
Making whittled wood balls in a cage
A classic trick toy, the ball-in-cage is a lose ball that is whittled to fit inside a wooden cage. To make one, you can use simple measuring, marking, and carving to make a smooth round surface. It is possible to carve a separate part within the outer box. This technique can be used to create intricate jewelry or a unique birdhouse.
Next, shape the ball once it's finished. A straight chisel is ideal for this process, as it provides greater control and makes it easier to cut along the end grain of the ball. To give the ball the desired shape, you can remove the bars from the cage. The final shaping is completed once the ball has become recognizable. To prevent any cuts from reaching the hands, you should sharpen your woodworking tools. Although gloves are not mandatory, they can be very useful.
FAQ
Do you have any other information I should know about woodworking and/or the process of making it?
It is easy for people to overlook the work involved in furniture making. Finding the right type of wood is the most difficult aspect of this process. It is difficult to choose between the various types of wood.
Another issue is that wood does not have the same properties. Woods can warp, split, or crack over time. These factors should be taken into account before buying wood.
How often should I purchase new supplies?
Some tools will need to be replaced over time. You'll need to sharpen your hand tools regularly if you use them. Power tools will require replacement parts every so often. Spread your purchases over several months to avoid purchasing too many items at once.
What is the difference in a hobbyist and professional woodworker?
Hobbyists like making things with wood. Professionals focus more on quality. Hobbyists often take pride in the creations they make and often share them to family and friends. Professionals will spend hours researching designs and then begin to create a project. They'll be meticulous about every aspect of their work, from choosing the best materials to finishing it perfectly.
How do you calculate woodworking costs?
The most important thing to remember when calculating costs for any project is to keep them as low as possible. It is important to ensure that you are getting the best materials prices. Also, consider all other factors that can affect the price of your projects such as skill level, experience, time and cost. Our guide to the average household DIY task price will give you an idea of how much it costs to complete different types of woodwork projects.
Do I need to be a genius to succeed in woodworking?
No. Woodworking does not require any special skills. To create stunning works of art, anyone can learn to use basic power tools.
How much should a woodworker charge per hour?
The hourly rate paid to a professional woodworker is dependent on many factors. These include skill level, availability, and location.
An hourly wage for skilled woodworkers is between $20 and $50.
A less skilled woodworker might charge as low as $10 per hour.
Statistics
- In 2014, there were just over 237,000 jobs for all woodworkers, with other wood product manufacturing employing 23 percent; wood kitchen cabinets and countertop manufacturing employing 21 percent. (theartcareerproject.com)
- Overall employment of woodworkers is projected to grow 8 percent from 2020 to 2030, about as fast as the average for all occupations. (bls.gov)
- Woodworkers on the lower end of that spectrum, the bottom 10% to be exact, make roughly $24,000 a year, while the top 10% makes $108,000. (zippia.com)
- Average lumber prices rose about 600 percent between April 2020 and May 2021. (familyhandyman.com)
External Links
How To
Here are some tips on how to drive nails in wood
When driving a nail into wood, it is important to first choose the correct size and kind of hammer. The most commonly used types of Hammers are claw hammers. Each type of tool has its advantages and drawbacks. A claw hammer, for example, is the best choice if you need to hit nails hard. However, it's not easy to know exactly where the impact will land. A sledgehammer is great for hitting large areas at once, but it's too heavy to use effectively for smaller tasks.
After choosing the right hammer, place your hand flat against the side of the head so that the handle rests comfortably in your palm. Grab the handle tightly, but do not squeeze too hard. Hold the hammer straight up, keeping your wrist relaxed. Then swing the hammer back toward the ground, aiming for the center of the nail. You should feel the impact of your hammer hitting the nail. You can practice swinging the hammer with a block or wood until you feel the rhythm.
You can now drive the nail by holding the hammer to your body. The nail should be perpendicular to wood's surface. Keep your focus on the tip of each nail. Swing your hammer forward. Then follow through with the motions of the hammerhead. This can be repeated several times to increase the speed of your swing. After mastering the technique, you can add power to your swings. Hold the hammer high above your shoulders and pull it down. This way, you'll be able to put more energy behind your blows.
Once you have successfully drilled the first hole in the nail, remove the hammer. You can then remove the rest of the nails using a prybar or a screwdriver. To avoid splitting the wood, make sure the nail heads are not touching the board's surface.