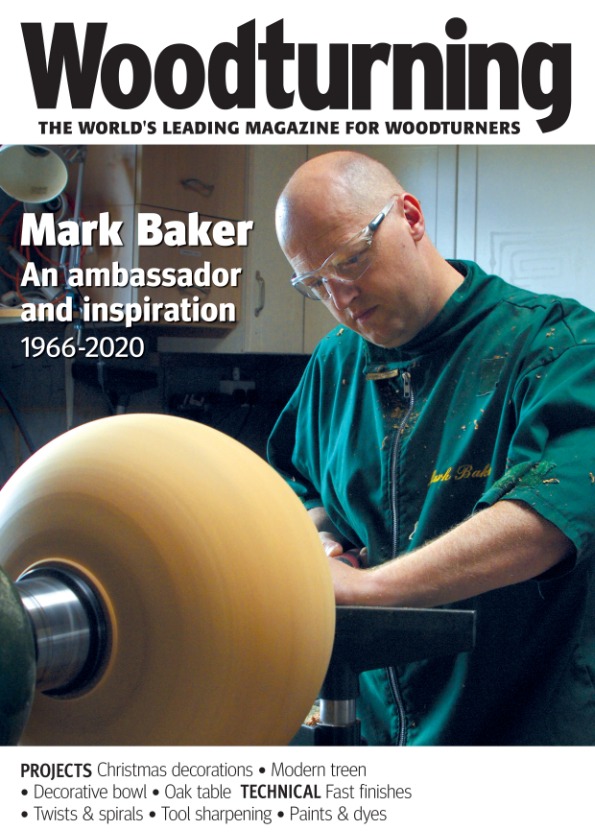
Philip Moulthrop, his father Ed Moulthrop, taught him how to turn wood in 1979. He uses a hand-forged, chainsaw and lathe to roughen out the green portions of trees from the Southeast. He then refines the bowl on the lathe, finishing it with several coats of finish. This entire process can take anywhere from 4 months to 1 year. The bowls can be bought or given as gifts once they are completed.
Philip Moulthrop
Phillip Moulthrop bowl, a magnificent red leopard maple vessel is available. The process of wood turning, which he developed, has been a family tradition for three generations. In addition to their own creations, Philip Moulthrop's bowls are part of the permanent collections of several prominent museums and private collections around the world. Below are some of the most well-known pieces. You can read more about this talented artist by reading the following.
Philip Moulthrop is an American artist who was born in 47. He was a student of general arts during his early 20s. However, he developed a keen interest in woodworking and a love for it later on. At the age of 16, he purchased his first machine and continued to improve his skills. He developed his techniques, producing beautiful turned vessels that attracted the attention of the art community and even the United States President. After his work had been recognized, he started selling his products at local craft shows and galleries. This earned him international recognition.
Matt Moulthrop
The Matt Moulthrop Boulbows are a fine example of Georgia’s rich wood-turning heritage. The artist was a Georgia Tech graduate. He was a skilled woodturner, even though he worked a lot in the 9-to-5 world for a while. He received national recognition for his bowls. His work is on display at ASU Art Museum, Carter Center, and Racine Art Museum.
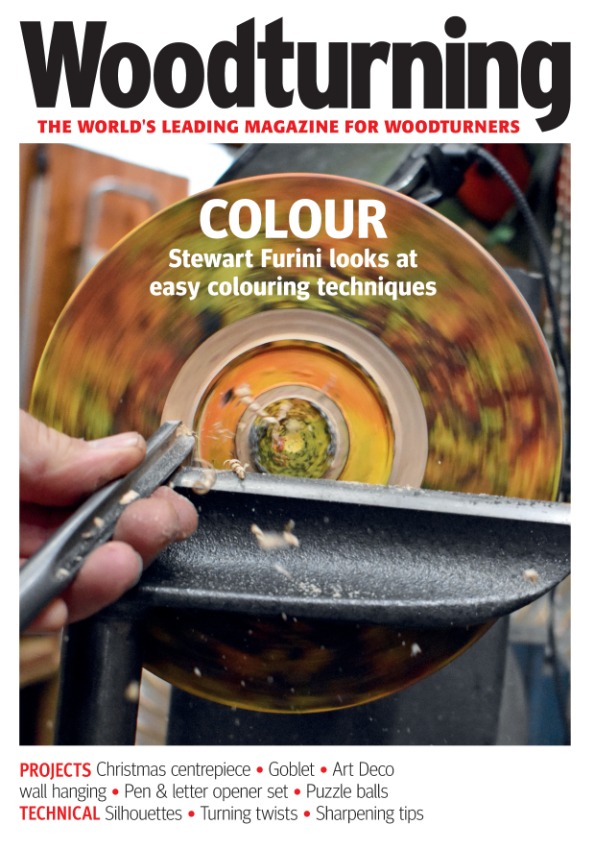
The Moulthrops have been recognized as world-class wood-turners, with works placed in prominent collections in the United States and abroad. Some of Moulthrop’s pieces are kept in the Renwick Gallery of the National Museum of American Art, which also includes his own. Collectors around the world have collected his bowls. He signed each photographer's copy of the family book during a Smithsonian photo shoot.
Ed Moulthrop
Moulthrop began to turn bowls around 1970s. Soon after, he received a scholarship at Princeton University to study architectural design. Moulthrop spent a year in Vietnam and then resigned as an architect to pursue woodturning. His large-scale turn bowls, which were internationally recognized, are now held in prestigious museums such as The White House Collection of American Crafts and Museum of Arts and Design. These bowls can be made from domestic woods or polished to a crystal clear finish.
This rare Ed Moulthrop bowl is nine inches in diameter by fourteen inches high and made of wild cherry. These wood bowls may be purchased at Gump’s in San Francisco. Many other Ed Moulthrop wood bowls are on display. The best way for you to learn more about this artisan is by visiting the exhibition. His work can also be found in a beautifully printed catalog. Although you can purchase his bowls at museums, it's better to visit his studio to actually see them in person.
The Eagle & Phenix Dam Series
This limited edition moulthrop series features wood from Eagle & Phenix Dam. A series of dams that once stood near Columbus, Georgia. The bowls have historical traces and were handcrafted in Atlanta by Philip and Matt Moulthrop. They are open for bidding during regular museum hours. Some bowls will be up for auction live.
The Moulthrop family has contributed to the growth of wood-turned bowls in Georgia. Three generations of Moulthrop have been turning bowls in Georgia for more than fifty decades. The museum is proud to display works from all three generations. Many of these pieces are prized due to their large size and smooth, polished surface. His unique mosaic bowl technique of glue and thin branches attached to a turned bowl is also featured in the exhibit.
Matt Moulthrop's works
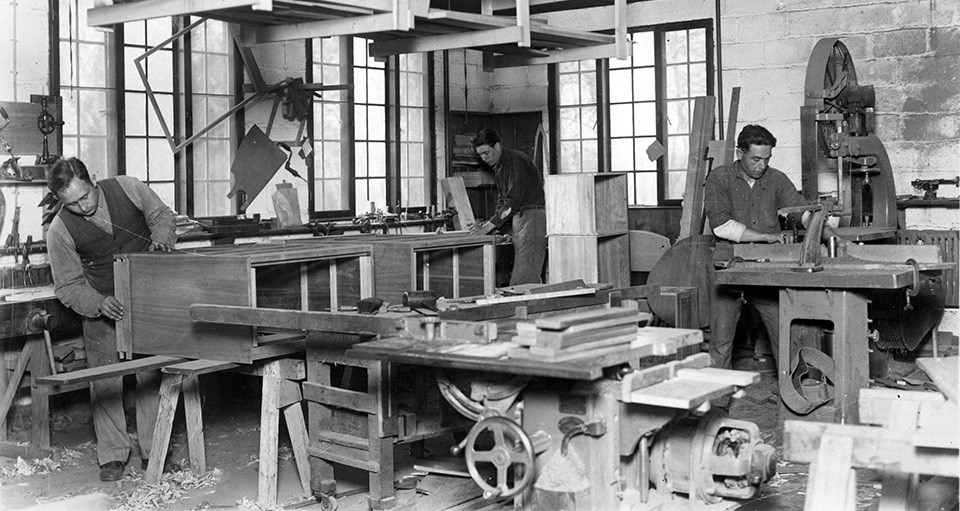
A son of Philip and Ed Moulthrop, Matt Moulthrop grew up around woodturning. His father was a pioneer in woodturning, and he continued to love it. Matt pursued a degree in business administration at Georgia Tech after earning his BA from the University of Georgia. He is now the third generation who makes wooden vessels. His work is included in numerous art institutions, including ASU Art Museum and Carter Center. He is currently working on commemorative pieces for the Georgia Tech Alumni Association's 100th anniversary.
Georgia is not home for the wood he transforms. To find unique wood, he travels all over the globe. He creates unique pieces by turning trees from around the globe with tools and a hand-forged, lathe. His pieces include wood harvested from trees that have fallen in the Southeast as also exotic locations such as volcanoes, underwater forests, and other places. Check out his work if you enjoy it!
FAQ
What tools should I start with when becoming a woodworker?
Woodworking takes practice and patience. It takes time to master all the tools and techniques involved in woodworking.
There are many types of woodworking equipment on the market today. Some people prefer to use power tools while others prefer manual tools.
You have the freedom to choose what tool you want, but it is important that you select the right tool for your job. It may be a good idea to start with a basic set, if possible, if you don’t know much about hand tools.
A router is a tool that cuts intricate shapes in wood. You can also learn how to use it. These can be found at most hardware shops.
Is there a way to start my own woodworking company?
It can be difficult to start your woodworking business. There are many laws and regulations you need to be aware of. However, it doesn't necessarily mean you must go through all the hassle of setting up a business. Many people prefer to join existing companies. You will only have to pay membership fees, taxes, and other charges.
Where do you start when it comes to woodworking?
Building furniture is the best way to learn how furniture is made. While you will need tools and make mistakes, you will eventually master the art of building furniture.
Choose a project that interests you. It can be something as simple and small as a box, or large-scale as an entertainment center. Once you have settled on a specific project, it is time to find a woodworker in your area who is experienced in such work. Ask him or her for advice on what tools you'll need and where to find them. Perhaps you could ask if there is someone else who does this type of work.
What type of wood should I choose?
The most commonly used woods for woodworking are oak, maple, cherry. Each type of wood has unique characteristics that affect the look and feel of the final product. Oak tends to be harder and darker than other woods. Birch is soft and light, and mahogany is denseer and heavier. You can also choose between solid wood and veneers. Veneers are thin sheets or wood that are glued together into one layer.
How much does a hobbyist need to invest in getting started?
If you're looking to start your own woodworking business, you'll probably need some capital to buy the necessary tools and supplies. You can start by purchasing a small table saw and drill press as well as a circular saw, circular saw, jigsaw and sanding machines. These items aren't very expensive, so you won't break the bank.
How often do I need to buy new supplies
You will likely need to replace some tools over time. Sharpening hand tools is a must. Power tools will require replacement parts every so often. Spread your purchases over several months to avoid purchasing too many items at once.
Statistics
- In 2014, there were just over 237,000 jobs for all woodworkers, with other wood product manufacturing employing 23 percent; wood kitchen cabinets and countertop manufacturing employing 21 percent. (theartcareerproject.com)
- Most woodworkers agree that lumber moisture needs to be under 10% for building furniture. (woodandshop.com)
- Average lumber prices rose about 600 percent between April 2020 and May 2021. (familyhandyman.com)
- Overall employment of woodworkers is projected to grow 8 percent from 2020 to 2030, about as fast as the average for all occupations. (bls.gov)
External Links
How To
How to make wood joints
This tutorial will demonstrate how to join two pieces together of wood. We will be using the "pocket-hole joint", which involves drilling holes in wood and then gluing them together. This works well if the wood is straight and smooth. You may want to consider other methods, such as dowel joining. These are the steps
-
Drill Pocket Hole Joints. To start, measure and mark where you want to put the pocket hole joint. With a handheld drill machine or jig saw, drill 3/4-inch deep holes in the ends of each piece.
-
Sand Smooth. The wood's edges can be sanded to prevent splitting.
-
Glue together. Apply glue to both the ends of the wood. Allow it to cool for at least 5 minutes before you attach the pieces.
-
Fix the Pieces together. After the glue has dried completely, you can clamp the pieces together until they are flush.
-
Trim Joinery. Trim the excess wood around the joint after the glue has dried completely.
To be able to turn the pieces inside-out, leave enough room between them.