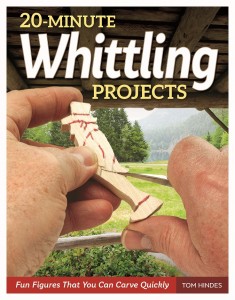
Seasoning wood is crucial to create safe and effective artwork, no matter if you are carving furniture or animal heads. Wood is easier to carve when it's still fresh and supple. But drying can pose a problem if the grain has spirals or is interlocked. Once you have seasoned the wood, you can apply shellac or paraffin wax to keep it flexible while you carve.
It is simple to carve green wood
If you're in the market for a piece of wood to carve, green wood is a great choice. Its softness and moisture make it easier to carve than other woods. It's perfect for carving bowls, spoons, or other items that have a bowl-shaped shape. The wood is soft but can split if it's not dried quickly enough. Try to avoid splitting branches by looking for those that will be less likely to split over time.
To prevent cracking, rotting, and decay of freshly cut greenwood, seal it properly. You can seal the wood with a commercial wood sealing agent such as ANCHORSEAL. Leave the wood piece for at least 2 weeks after applying the sealant. This will help protect the wood from the weather and keep it fresh. It is important to remember that green wood is softer than dried wood, so you may have to make some repairs to avoid cracking.
Carving dry wood can be more difficult
Special tools are needed to moisten dry wood when carving. Wood purchased from a shop usually has a moisture content between 10-20%. Commercial wood manufacturers dry wood much faster than it can naturally dry. Therefore, wood purchased for carving will often be green or still green. Generally, green wood is easier to carve than dry wood.
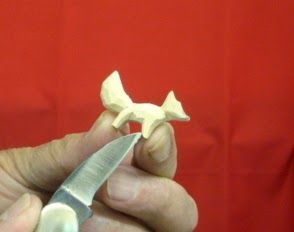
It becomes harder to carve wood that has a lower moisture content. This causes the blade to dull quicker. Also, when the wood is dry, the tool will be less likely to break if you accidentally hit it. This makes it harder to maintain. This is why it is best to buy greenwood from a reputable shop. You can save money and avoid the hassle of storing green wood.
Drying problems can be caused by interlocked or spiral grain
Seasoning wood for carving with interlocked or spiral-grain can cause drying problems, unlike traditional hardwoods that dry quickly. Additionally, this wood is more susceptible to warping than other types. To avoid this, store it in dry, cool places. Maple is the best wood to carve.
Red oak is an excellent choice for carving, since its heartwood is light to dark red, with a faint purple tint. It has a rough texture and a slight luster. It has a low odor and an air-dry density of 25 to 40 ppf. The Janka side hardness of red oak is between 570 and 665 lb for dry materials and 210 to 218, respectively, for green wood.
Paraffin wax and shellac applied to wood prior to carving
Apply a sealer after you have removed the bark from your wood to carve. You can use either shellac or paraffin wax. It should be applied around the ends of the wood. It will also add durability and protection from the elements. It is important to apply three to four coats of sealer to the wood you are using for carving.
Before applying shellac, sand the wood surface with finer sandpaper. This will make the surface smooth and free of any ridges. It will be much easier to sand your piece after the shellac has dried. Apply three to four coats of shellac to your wood for best results. For wood with a rough surface, 400-grit paper is recommended. The final coat is largely for appearance and function.
Avoid knots

Before carving an animal, stick, or any other object, you need to season the wood first. Seasoning is the process that removes water from wood. Modern methods can reduce the seasoning time to a matter of weeks, but it's still important to avoid wood that has large knots. They can cause warping and cracking.
You can always test the wood before you start. The best wood for carving spoons is green. You can also get it from your friends and neighbors for free. You should choose wood at least three times the thickness of your spoon when you are choosing wood. Although you can also find green wood in the market, make sure it isn't too hard. As you become more skilled, you will be able to season harder timber.
FAQ
How do I calculate woodworking prices
It is crucial to keep project costs as low-cost as possible. You should always try to make sure that you are getting the best deal on materials. It is important to take into consideration all factors that can impact the cost of your projects. These include time, skill and experience. Check out our guide on the average cost of common DIY projects to get an idea of how much you can spend on woodwork projects.
Where can I find free woodworking plan?
You don't need to purchase any books or magazines to find free woodworking plans. You just need to search Google. Enter "free woodworking", and you will see hundreds upon hundreds of websites offering free plans.
How can I tell what kind of wood I am working with?
Always read the label when purchasing wood. The label should include information about the wood species and its moisture content as well as whether or not it has been treated using preservatives.
How can my shop be organized?
First, make sure you have a designated space for tools storage. Keep your tools away from dust and debris, so they stay sharp and ready to work. You can hang tools and accessories with pegboard hooks.
Statistics
- Average lumber prices rose about 600 percent between April 2020 and May 2021. (familyhandyman.com)
- The U.S. Bureau of Labor Statistics (BLS) estimates that the number of jobs for woodworkers will decline by 4% between 2019 and 2029. (indeed.com)
- Woodworkers on the lower end of that spectrum, the bottom 10% to be exact, make roughly $24,000 a year, while the top 10% makes $108,000. (zippia.com)
- Most woodworkers agree that lumber moisture needs to be under 10% for building furniture. (woodandshop.com)
External Links
How To
How to stain wood
Stain wood is a process that involves applying chemicals to the surface of wood, which changes its color. The wood will turn from white to brownish-red due to the chemical reaction. Oak is the most common wood type for staining. However, you can also use other wood types.
There are several ways to apply stains to wood surfaces. Some methods involve mixing the stain with a solvent (such as turpentine) and then brushing or spraying the mixture onto the wood. You can also apply a solution containing water and dye directly to the wooden surface. The stain can be mixed with paints and varnishes to become part of the final coating.
Preparing your wood for staining is the first thing to do. To apply the stain, clean the wood completely. Sanding smoothens any scratches or rough spots. The next step is to determine the type of stain you would like to use. There are two types of stains that can be used: penetrating and non-penetrating. Penetrating stains penetrate deeper into the wood than non-penetrating ones, making them ideal for dark colors such as mahogany. Light colors such as maple work well with non-penetrating stain.
You will need to decide on the type of stain you want to use, and then prepare your tools. Paintbrushes are great for applying stain because they allow you to evenly spread the liquid across the surface. It is a good idea to have rags on hand in case you need them to clean up any stains that may remain after you have finished painting. If you are planning to mix your stain, ensure you have enough containers for each component.
After you have prepared the materials, you can clean the area where you want to stain the wood. You can remove grime and dirt with warm water and soap. Use a dampened sponge and warm water to clean the entire piece. You should remove any debris, especially if your plan is to stain darker wood.
The stain should be applied next. Begin at one end and spray or brush the stain on the wood. You should work slowly and carefully. Continue moving along the grain until you reach your opposite end. Keep the stain from dripping off the wood's surface. Allow the stain to dry completely before you move on to the next step.
Protect the painted surface with a coat polyurethane paint sealant. Three coats of polyurethane sealing agent are required. Allow the third coat to dry overnight before sanding the final coat.